I costi dell’acciaio verde
La transizione ecologica dell’industria siderurgica comporta diverse sfide tecniche, economiche e sociali. Come le stiamo affrontando?
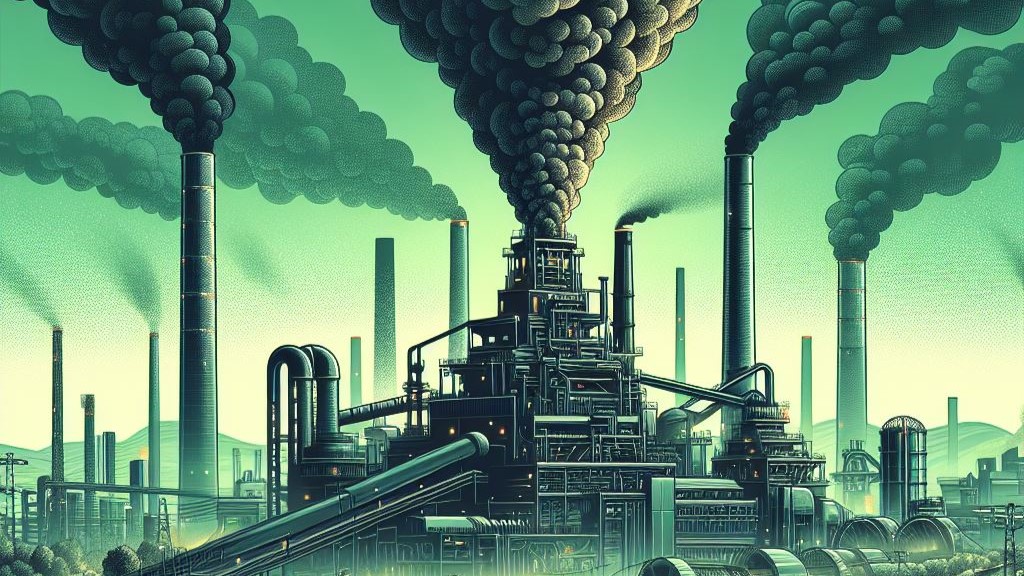
Tra giugno e settembre 2024, gli altiforni dell’acciaieria Tata Steel di Port Talbot, in Galles, verranno spenti per sempre. La Tata Steel, multinazionale indiana del siderurgico, ha annunciato che saranno sostituiti con dei forni elettrici, meno impattanti sull’ambiente. La trasformazione porterà, secondo le stime dei sindacati riportate dal Guardian, la perdita di 2800 posti di lavoro. Quelli, al contrario degli altiforni, non saranno sostituiti.
Come mostra il caso di Port Talbot, la transizione ecologica dell’industria siderurgica è un percorso tortuoso. Parte dall’abbandono del carbone, finisce l’idrogeno verde e, nel mezzo, richiede un aumento dell’uso del gas e un calo degli occupati, perché per i forni elettrici serve meno manodopera.
Oggi, la produzione di acciaio in Ue vale il 5% delle emissioni (7% a livello globale) e 2.5 milioni di posti di lavoro tra diretti, indiretti e indotto. Come il trasporto aereo, è uno dei settori definiti hard to abate, cioè le attività con le emissioni di CO2 più difficili da ridurre. L’arrivo a una produzione di solo acciaio “verde” è una sfida complessa che tocca aspetti tecnologici, economici e sociali. Proviamo a capire se e come l’Europa li sta affrontando.
L’acciaio oggi: come si fa e quanto impatta
Nel 2024 l’acciaio si produce in due modi.
C’è la siderurgia primaria, o ciclo integrale, che utilizza gli altiforni: questi enormi impianti sempre accesi combinano il minerale di ferro con il coke, cioè carbone cotto, per produrre ghisa liquida, che poi viene convertita in acciaio primario da un forno a ossigeno di base. È il metodo tradizionale, quello che la Tata Steel abbandonerà a Port Talbot.
Poi c’è la siderurgia secondaria: dei forni elettrici ad arco fondono il rottame, cioè dei rifiuti ferrosi, per produrre acciaio. L’acciaio è infatti un materiale completamente riciclabile.
La produzione con altiforni offre un acciaio più puro ma ha un enorme impatto ambientale. Secondo uno studio sulla decarbonizzazione dell’industria siderurgica della Fondazione Di Vittorio, un ente di ricerca della CGIL, la produzione di una tonnellata di acciaio genera con il ciclo integrale oltre 2 tonnellate di CO2, a fronte di 0.135 tonnellate con i forni elettrici. Il ciclo integrale comporta anche maggiori consumi di acqua e suolo, mentre i forni elettrici hanno, ovviamente, consumi di energia più alti.
Questo grafico mostra il confronto dell’impatto su emissioni e consumi dei due modelli di produzione.
Il ciclo integrale è il modello più diffuso nella siderurgia mondiale, dominata dalla Cina. Mentre l’Italia, il secondo produttore di acciaio in Europa, si trova in una situazione inversa: Taranto è l’unica città dove si fa ancora acciaio primario con altiforni, con circa il 16.5% della produzione nazionale. Il resto dell’acciaio viene fatto nei forni elettrici, soprattutto da PMI lombarde.
Come si rende l’acciaio verde?
Il problema è complesso. Per raggiungere l’obiettivo europeo di taglio dell’80-95% delle emissioni del siderurgico nel 2050, non c’è una soluzione unica e pronta su larga scala, ma serve l’adozione contemporanea di più strategie.
Una è favorire il riciclo dell’acciaio, aumentando sempre di più la siderurgia secondaria che, come visto, inquina meno. Un’altra è la creazione di sistemi di cattura e stoccaggio dell’anidride carbonica, cioè quelle tecnologie, ancora in fase sperimentale, con cui si spera di poter compensare tutte le emissioni non rimovibili.
Altra strada importante è l’aumento dell’uso del preridotto o DRI (Direct Reduced Iron): si tratta di un materiale ferroso che subisce una riduzione diretta con gas naturale, carbone o idrogeno, senza dover passare attraverso la fusione. Può essere impiegato sia negli altiforni sia nei forni elettrici al posto del rottame, in entrambi i casi con minori emissioni climalteranti.
Se poi la riduzione del DRI avviene con idrogeno verde, prodotto da fonti rinnovabili, le emissioni sono nulle: il minerale ferroso (ossido di ferro) non cede più l’ossigeno al carbonio producendo CO2, ma all’idrogeno, producendo acqua. In questo caso, è quindi corretto parlare di “acciaio verde”, realizzato con zero emissioni di anidride carbonica.
Pulito e competitivo? I tentativi dell’Ue
L’acciaio prodotto da DRI e idrogeno verde nei forni elettrici è l’obiettivo finale della strategia Ue per la decarbonizzazione del settore siderurgico, ma la strada è ancora lunghissima: oggi, l’acciaio verde viene fatto soltanto da progetti pilota con produzioni limitate, in particolare nel Nord della Svezia, dove c’è alta disponibilità di rinnovabili. Al 2030, il piano REPowerEU punta a rendere “verde” circa il 30% dell’acciaio primario.
Tutto questo va poi fatto mantenendo la competitività della siderurgia europea, già in crisi per il caro energia causato dalla guerra in Ucraina. È possibile? I problemi sono tanti e di varia natura, come emerso durante il convegno di Legambiente “L’acciaio oltre il carbone” a Taranto.
C’è intanto un tema di materie prime. Abbandonare gli altiforni per i forni elettrici richiede una crescita della domanda del materiale ferroso per gli impianti DRI e di rottame di acciaio, entrambi poco disponibili sul mercato. Vuol anche dire aumentare i consumi di gas, prima, e di energia rinnovabile, poi, con tutte le relative incognite legate ai costi. La filiera dell’idrogeno verde, su cui l’Europa sta comunque investendo molte risorse, è di fatto un mercato ancora da costruire.
La stessa Ue riconosce che i costi di produzione dell’acciaio da DRI e idrogeno verde potrebbero diventare competitivi soltanto intorno al 2050, quando, si presume, i costi delle rinnovabili saranno minori e produrre con fonti fossili non converrà più. A livello normativo, due misure dovrebbero aiutare il siderurgico in questo senso.
La prima è l’ETS (Emission Trading System), il sistema internazionale di scambio di quote di emissioni di CO2 tra le aziende più inquinanti: in pratica, gli impianti ETS, tra cui le acciaierie, possono acquistare o vendere quote per emettere tonnellate di CO2, mentre un tetto stabilisce la quantità massima di quote del sistema. Di anno in anno, il tetto del sistema scende e i prezzi delle quote di CO2 salgono, incentivando le aziende ad essere sempre più virtuose.
La seconda è il CBAM (Carbon Border Adjustment Mechanism), che consiste in una sovrattassa sulle importazioni europee dei beni realizzati con un’alta quota di CO2. Il regime definitivo del CBAM entrerà in vigore nel 2026, per bilanciare una nuova fase dell’ETS più ambiziosa e quindi più stringente per le aziende inquinanti. È una misura che tutela il mercato interno, togliendo il vantaggio all’acciaio più economico dei paesi extra Ue con politiche green meno rigide. Tuttavia, lascia aperto il problema degli export.
«Il CBAM protegge dalle importazioni, ma l’extra costo green delle acciaierie come potrà essere protetto dall’Unione Europea? In futuro, riusciremo ancora a esportare acciaio?» chiedeva durante il convegno Stefano Ferrari, responsabile dell’ufficio studi di Siderweb, quotidiano nazionale dedicato all’informazione economico-siderurgica.
Rispondere è prematuro, anche perché l’impianto di queste e altre misure del Green Deal rischia di essere rivisto dalla nuova maggioranza che si formerà dopo le elezioni europee.
Elezioni che saranno anche animate dal tema della falsa contrapposizione tra ambiente e lavoro. Falsa, appunto, almeno per il circa 95% degli occupati in Ue, cioè tutti quelli che non sono impiegati nei cosiddetti “lavori marroni”, più impattati dalla transizione. Ma chi lavora negli altiforni non è in quel 95%.
E i lavoratori?
Come detto, saranno meno, perché i forni elettrici richiedono meno manodopera del ciclo integrale.
Di quanto? «Secondo la letteratura più tecnica, la produzione di 1 milione di tonnellate di acciaio con forno elettrico richiede fra i 227 e 400 lavoratori, molti di meno rispetto al migliaio circa con il ciclo integrale» ha spiegato a Slow News Lidia Greco, sociologa esperta di transizione energetica e autrice del precitato studio della Fondazione Di Vittorio. Il calo di più o meno due terzi è in linea con le cifre denunciate dai sindacati della Tata Steel di Port Talbot: da 4000 a 1200 lavoratori, cioè un taglio di manodopera del 70%.
Mentre scriviamo è il 10 maggio 2024 e migliaia di lavoratori della Tata Steel hanno appena lanciato uno sciopero. Intanto, in Ue (e in Italia molto piano) ha preso il via il programma Just Transition Fund, pensato per tutelare i lavoratori e i territori che più soffriranno la transizione.
Ma, come abbiamo raccontato qui, la sfida è enorme: la transizione energetica non sarà per forza giusta e non sarà un pranzo di gala.
**
L’immagine di copertina è realizzata con Dall-e.